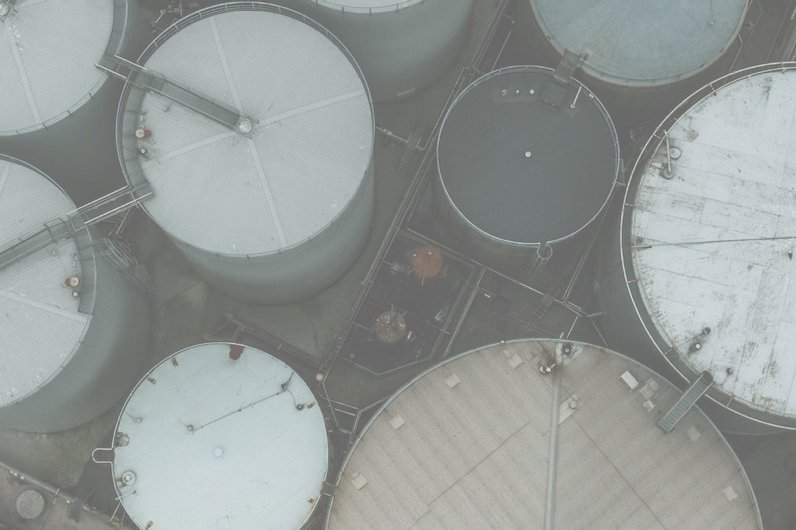
L’inspection basée sur la criticité (IBC ou RBI)
Par Armand Gilly
Le 16/03/2023
Les services inspection doivent s’assurer de l’intégrité et de la conformité de chacun des équipements du site industriel dont ils ont la responsabilité.
Pour y parvenir, il est nécessaire d’inspecter chacun des équipements régulièrement. Les types de contrôle et leur fréquence sont déterminés par les responsables inspection tout en étant encadrés par la législation.
Comme tout service, les moyens du service inspection sont limités et il faut prioriser les actions à faire tout en s’assurant du respect de la législation et de la sécurité des installations.
Une des méthodes permettant de prioriser et de définir les fréquences de contrôle des équipements statiques d’un site industriel est l’Inspection Basée sur la criticité (IBC) ou Risk Based Inspection (RBI) en anglais. Celle-ci vise notamment à prendre en compte la probabilité d’occurrence d’un accident et sa gravité potentielle comme données d’entrée pour prioriser les contrôles à effectuer ainsi que leur fréquence. Cette approche permet de concentrer les efforts d’inspection sur les équipements qui présentent les risques les plus élevés, réduisant ainsi les coûts et améliorant la sécurité.
Explication de la méthode RBI
Il n’existe pas une méthode RBI unique. La méthode dépend du référentiel choisi (API 580, API 581, UFIP, ASME, UIC…). Toutefois la logique reste similaire et il est possible de généraliser ces méthodes de la manière suivante.
Tout d’abord une liste de tâches à réaliser de manière séquentielle permet de déterminer le plan d’inspection.
1. Identification des équipements à risque
La première étape de l'inspection basée sur la criticité consiste à identifier les équipements les plus critiques.
Plus un équipement a un risque d’occurrence d’un accident grave élevé, plus il est considéré comme étant critique. Un accident est considéré comme étant grave s’il peut causer des dommages graves à l'environnement, aux travailleurs ou à l'entreprise elle-même.
Les équipements définis comme étant critiques sont ainsi intégrés à la méthode. Cette sélection s’appuie le jugement d’experts du domaine. Un groupement par type d’éléments ou par type de dégradation peut être réalisé pour l’analyse.
2. Détermination des modes de dégradation et des scénarios de défaillance
Pour chaque équipement ou groupement d’équipements sélectionnés, il faut déterminer les modes de dégradation et scénarios de défaillance. Ce travail est réalisé par des experts du domaine à partir de leur retour d’expérience et de leurs connaissances métier.
3a. Détermination de la probabilité d’occurrence de la défaillance
La probabilité d’occurrence d’une défaillance dépend de plusieurs facteurs et notamment de l’état de l’équipement. Ainsi, pour la déterminer, les experts se basent sur des données génériques augmentées ou diminuées en fonction des défauts relevés lors de la dernière inspection.
Le service inspection peut par la suite faire varier cette probabilité en effectuant des travaux modificatifs sur les équipements à risque.
3b. Détermination de la gravité potentielle de la défaillance
Pour déterminer le niveau de gravité, les experts du domaine se basent surtout sur leurs connaissances et retours d’expérience.
4. Estimation de la criticité pour chaque équipement
Par la suite il est possible de déterminer la criticité de chaque mode de dégradation ou scénario de défaillance des équipements ou groupements d’équipements sélectionnés.
Cette criticité est évaluée en fonction de la probabilité d’occurrence de la défaillance et de la gravité potentielle des conséquences de la défaillance. Une matrice Gravité / Probabilité permet généralement d’obtenir la valeur de la criticité.
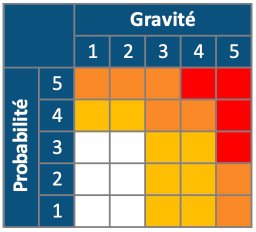
5. Déterminer le plan d’inspection
Une analyse permet, par la suite, de hiérarchiser les équipements en fonction de leur criticité et de définir un plan d’inspection approprié.
Ces plans d’inspection contiennent la qualité minimale des contrôles à effectuer (points de contrôles, type d’inspection …) ainsi que les durées maximales entre inspections. Ces données sont déterminées en fonction de la criticité, de l'historique des défaillances et des conditions d'exploitation.
Ce travail doit permettre de limiter les risques tout en diminuant les inspections et donc les coûts de contrôle. Ceci est possible en focalisant les efforts sur les équipements les plus critiques.
Nota : les amplitudes de contrôle maximales entre 2 inspections (notamment pour les ESP) sont définies par la législation.
Aussi, des tâches sont réalisées en parallèle et influent sur les tâches précédentes :
6. Évaluation de l’endommagement
Le niveau d’endommagement par rapport au mode de dégradation est évalué à chaque inspection. Ainsi, chaque inspection permet de réévaluer la probabilité d’occurrence d’une dégradation et de redéfinir la valeur de la criticité.
Les inspections peuvent être effectuées en réalisant des Contrôles Non Destructifs (CND), comme les ultrasons, le ressuage ou la thermographie. Ces méthodes permettent de détecter les défauts avant qu'ils ne deviennent critiques. Les résultats des inspections doivent être enregistrés pour suivre l'évolution de l'état de l'équipement.
7. Optimisation et amélioration
Une fois que toutes les étapes prédécentes ont été réalisées, il est possible de diminuer le niveau de criticité des défaillances en réalisant des modifications mécaniques ou de procédé, sur les équipements les plus critiques.
Avantages de l'inspection basée sur la criticité
L’Inspection Basée sur la Criticité est une approche rentable, car elle permet de concentrer les efforts de contrôle et d’inspection sur les équipements qui présentent les risques les plus élevés. En focalisant les efforts, il est possible d’économiser en limitant le nombre de contrôles et en limitant les temps d’arrêt ce qui a pour effet d’optimiser la production.
L’inspection basée sur la criticité n’a pas pour seuls avantages la réduction des coûts d’inspection et l'optimisation de la production. Elle permet également d'améliorer la sécurité des travailleurs et des installations en identifiant les équipements les plus critiques et en garantissant leur fiabilité.
Les logiciels RBI
Pour aider les services inspection dans la mise en place et le suivi d’une méthodologie RBI des logiciels existent. Ils permettent notamment de définir la criticité et d’établir des plans d’inspection.
Ces logiciels sont conseillés pour les experts du métier et peuvent être complétés par d'autres logiciels pour les aider dans leurs tâches quotidiennes.
Ealico, le complément idéal à un logiciel de RBI
Les services inspection, équipés d’un logiciel RBI ou non, peuvent utiliser un Logiciel de Maintenance Réglementaire (LMR) tel que Ealico pour s’assurer de la conformité réglementaire de leurs équipements.
Les obligations réglementaires sont déterminées automatiquement, les évolutions réglementaires sont prises en compte sans nécessiter l’intervention de l’utilisateur, les observations (ou non-conformités) issues des rapports de contrôles sont centralisées, peu importe l’organisme intervenant, un plan d’action permet aux responsables d’avoir une vision claire des actions à mener pour atteindre le niveau de conformité souhaité.
Avec Ealico, les responsables peuvent se concentrer réellement sur l’expertise métier pour atteindre un niveau de conformité et de sécurité de leurs installations optimal.